Produktion
Unser globales, markenübergreifendes Produktionsnetzwerk stellt die Prozesse vom Lieferanten zur Fabrik und Montagelinie sowie aus der Fabrik zum Handel und zum Kunden sicher. Eine dauerhafte Effizienz ist Voraussetzung für unsere Wettbewerbsfähigkeit. Mit ganzheitlichen Optimierungen, zukunftsgerichteten Innovationen, flexiblen Lieferströmen und Strukturen sowie einer agilen Mannschaft begegnen wir den Herausforderungen der Zukunft. Im Geschäftsjahr 2018 übertraf die weltweite Fahrzeugfertigung mit 11,0 Mio. Einheiten den Vorjahreswert. Trotz anhaltend schwieriger Rahmenbedingungen in vielen Märkten nahm die Produktivität im Vergleich zum Vorjahr um rund 5,3 % zu.
Produktionsstrategie „Intelligent vernetzt“
Die Produktion unterstützt das Zukunftsprogramm „TOGETHER – Strategie 2025“ mit ihrer Funktionalbereichsstrategie „Intelligent vernetzt“. Durch die intelligente Vernetzung von Menschen, Marken und Maschinen wollen wir die Kräfte und Potenziale unserer weltweiten Fertigung und Logistik bündeln und dadurch Synergien erschließen. Die Leitplanken sind unsere vier strategischen Zielfelder:
- Wandlungsfähiges Produktionsnetzwerk
- Effiziente Produktion
- Intelligente Produktionsprozesse
- Zukunftsfähige Produktionsarbeit
Mit geschäftsbereichsspezifischen Initiativen haben wir inhaltliche Cluster gebildet, in denen kompetenzstarke Teams die für die Produktion im Konzern relevanten strategischen Themen bearbeiten. Die wettbewerbsfähige Gestaltung unseres weltweiten Produktionsnetzwerks, die Reduzierung und der Ausgleich von Umweltbelastungen entlang des Produktionsprozesses sind ebenso Beispiele wie die Digitalisierung mit ihren Auswirkungen auf Produktions- und Arbeitsprozesse sowie auf die Zusammenarbeit. Übergreifendes Ziel ist es, die Produktivität und die Profitabilität zu steigern.
Mit der Produktionsstrategie haben wir die Basis für eine erfolgreiche und nachhaltige Weiterentwicklung unserer Produktion geschaffen. Mit regelmäßigen Reviews stellen wir sicher, dass wir unsere Aktivitäten laufend an den aktuellen Herausforderungen ausrichten.
Globales Produktionsnetzwerk
Mit zwölf Marken und 123 Produktionsstandorten sind einheitliche Standards für Produktkonzepte, Anlagen, Betriebsmittel und Fertigungsprozesse ein wichtiger Bestandteil der zukunftsorientierten Fertigung. Diese Standards ermöglichen es uns, Synergien zu erzielen, flexibel auf Marktanforderungen zu reagieren, ein flexibles Produktionsnetzwerk optimal auszulasten sowie Mehrmarkenstandorte zu realisieren. Aktuell sind bereits knapp die Hälfte der 45 Pkw-Standorte Mehrmarkenstandorte. Ein Musterbeispiel ist weiterhin der Standort Bratislava: Hier werden Fahrzeuge der Marken Volkswagen Pkw, Audi, Porsche, SEAT und ŠKODA produziert. Der jüngste Mehrmarkenstandort ist Wolfsburg, wo im Herbst 2018 die Produktion des SEAT Tarraco anlief.
Der Volkswagen Konzern hat sich zum Ziel gesetzt, bis 2025 ein weltweit führender Anbieter batterieelektrischer Fahrzeuge zu werden. Grundlage hierfür ist die Einführung des Modularen E-Antriebs-Baukastens MEB. Mit ihm werden wir unser Angebotsportfolio um weitere batterieelektrische Fahrzeuge ergänzen.
Um Mehrmarkenprojekte und Elektromobilität in Verbindung mit bestehenden Konzepten wirtschaftlich zu gestalten, ist es wichtig, die Fertigung höchst flexibel und effizient auszurichten. Außerdem ist die maximale Nutzung von Synergiepotenzialen ein entscheidender Faktor für den Erfolg künftiger Fahrzeugprojekte. Der Einsatz von gleichen Teilen, Konzepten sowie Fertigungsprozessen ermöglicht die Reduzierung von Investitionen und die Chance, vorhandene Kapazitäten besser auslasten zu können. In Zukunft werden elektrifizierte Fahrzeugprojekte an Mehrmarkenstandorten hinzukommen, zum Beispiel in Zwickau und im chinesischen Anting.
Wir entwickeln unsere Produktionskonzepte stetig weiter und richten sie auf neue Technologien aus. Dabei dient der in der Strategie verankerte Targetierungsprozess der Realisierung von ambitionierten Zielen in den einzelnen Projekten in einem geschäftsbereichsübergreifenden Vorgehen.
Produktionsstandorte
Das Produktionsnetzwerk des Volkswagen Konzerns umfasst 123 Standorte, an denen Pkw, Nutzfahrzeuge und Motorräder sowie Aggregate und Komponenten gefertigt werden.
FAHRZEUGPRODUKTIONSSTANDORTE DES VOLKSWAGEN KONZERNS
Anteil an der Gesamtproduktion 2018 in Prozent
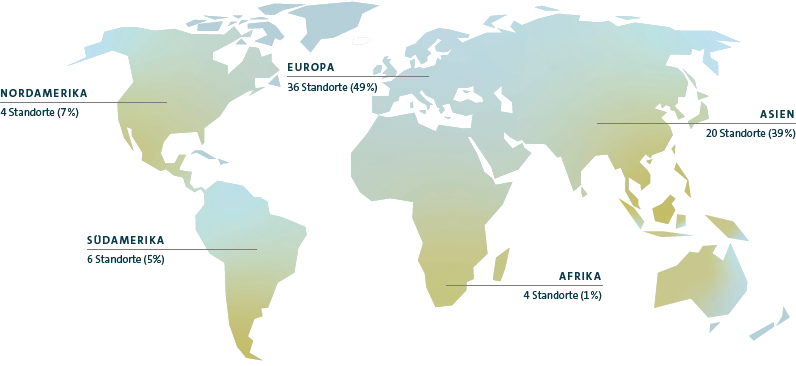
Mit 71 Standorten bleibt Europa unsere wichtigste Produktionsregion für die Fertigung von Fahrzeugen und Kom-ponenten. Allein in Deutschland befinden sich 28 Standorte. Die Region Asien-Pazifik hat 34 Standorte. In Nordamerika sind es fünf und in Südamerika neun Standorte. In Afrika betreibt der Konzern vier Standorte.
In 2018 haben wir 52 Produktionsanläufe durchgeführt, davon waren 29 neue Produkte beziehungsweise Produktnachfolger sowie 23 Produktaufwertungen oder Derivate.
Die Auslastung der Standorte im Produktionsnetzwerk des Volkswagen Konzerns wird durch die Belieferung mit Teilesätzen als Completely-Knocked-Down (CKD)-Standort weiter gestärkt.
Das Konzern-Produktionssystem
Unser Ziel ist die kontinuierliche und nachhaltige Verbesserung unserer Abläufe an allen Standorten der Marken und Regionen. Ein wesentlicher Baustein zur Erreichung exzellenter Prozesse in der Produktion und im produktionsnahen Umfeld ist das Konzern-Produktionssystem, das wir weiter festigen und dessen Durchdringungsgrad wir erhöhen.
Im Vordergrund stehen dabei die Themen Führung sowie Verantwortung des Einzelnen, die in eine Kultur der wertschätzenden Zusammenarbeit eingebettet sind.
Für die Erreichung des Ziels, weiterhin Produkte mit hoher Qualität und hohem Kundennutzen zu wettbewerbsfähigen Kosten fertigen zu können, muss eine Fabrik optimal ausgelastet werden. Möglich wird das durch eine frühzeitige Standardisierung von Fertigungsprozessen und Betriebsmitteln. Grundlage hierfür ist die sogenannte Konzeptgleichheit: Sie sorgt dafür, dass in den Entwicklungs- und Produktionsbereichen der Marken gemeinsame Konstruktionsprinzipien, Fügetechniken und Fügefolgen, aber auch Verbau- und Anbindungskonzepte angewandt werden. Mit Hilfe der Konzeptgleichheit wird ein Fundament geschaffen, auf dem effiziente Logistik- und Fertigungsprozesse gestaltet werden können.
Neue Technologien und Produktionsinnovationen
Der 3D-Druck ist eine der Schlüsseltechnologien von Industrie 4.0 und der Digitalisierung der automobilen Wertschöpfungskette. Das Verfahren eröffnet in den Bereichen Entwicklung, Design und Produktion völlig neue Möglichkeiten. Aufgrund des digitalen Charakters der Technologie, die keinerlei Werkzeuge benötigt, lassen sich Bauteile flexibel und direkt aus digitalen Zeichnungen umsetzen sowie gänzlich neue Designs und Bauteilgeometrien verwirklichen. Die Technologie des 3D-Drucks wird bereits seit vielen Jahren erfolgreich zur Erstellung von Prototypen verwendet und zeigt in den letzten Jahren eine rasante Weiterentwicklung, welche auch mit neuen Anwendungsfeldern bei Volkswagen einhergeht. Die Besonderheit dieser Technologie, auch „additive Fertigung“ genannt, liegt im Einfluss entlang der gesamten automobilen Wertschöpfungskette. Sie reicht von der Anwendung für frühe Designstudien, in der Prototypenfertigung, für Werkzeuge und Betriebsmittel, für Kleinserienteile bis hin zur Herstellung von Ersatzteilen im After-Sales-Bereich. Die für den 3D-Druck verfügbaren Materialen reichen von Kunststoffen über Faserverbundmaterial bis hin zu metallischen Werkstoffen.
Der Weg in Richtung Großserienanwendungen im Automobilbau ist jedoch noch weit. Volkswagen nutzt hier durch enge Zusammenarbeit seiner Marken die Vielfalt des Konzerns und arbeitet mit führenden Technologieanbietern und Forschungseinrichtungen zusammen. So setzt beispielsweise die Marke Volkswagen Pkw in Kooperation mit dem Druckerhersteller HP und dem Bauteilproduzenten GKN Powder Metallurgy als erster Automobilhersteller auf die neueste 3D-Druck-Technologie „HP Metal Jet“.
Bei der Konzeption und Einführung von neuen Technologien in der Produktion werden die betroffenen Mitarbeiter von Beginn an in die Umgestaltung der Arbeitsplätze und der Abläufe einbezogen. Das ist eine wichtige Voraussetzung für die erforderliche Akzeptanz der neuen Technologien und Lösungen.
Umwelteffiziente Fertigung
Ein Element der Produktionsstrategie ist die Initiative Ökologisch vorbildliche Produktion. Hier arbeiten wir bis 2025 an vier Schwerpunktthemen:
- Setzen und Erreichen von ambitionierten Umweltzielen für die Produktion
- Erarbeiten und konzernweites Ausrollen einer langfristigen Vision der Umweltziele in der Produktion
- Stärken des Umweltbewusstseins der Mitarbeiter und Integration von relevanten Umweltaspekten in Prozessen
- Erreichen von Spitzenplätzen bei namhaften Umweltrankings
In diesem Rahmen hat sich der Volkswagen Konzern zum Ziel gesetzt, in der Produktion die fünf Umweltkennzahlen Energie- und Wasserverbrauch, Abfälle zur Beseitigung sowie CO2- und VOC-Emissionen je produziertes Fahrzeug – ausgehend vom Stand des Jahres 2010 – bis 2025 um 45 % zu verringern. Dieses Ziel gilt für alle Produktionsstandorte des Konzerns, abgeleitet aus unseren ökologischen Anforderungen an die Fertigungsprozesse, die in den Umweltgrundsätzen des Konzerns verankert sind. Die oben stehenden Grafiken zeigen die Entwicklung dieser Indikatoren.
Wir fördern weltweit die Vernetzung und den Austausch zwischen den Marken, um Synergien zu heben. Unsere Umweltexperten treffen sich regelmäßig in Arbeitsgruppen; außerdem schulen wir unsere Mitarbeiter zum Thema Umweltschutz.
Um standortspezifische Einsparmaßnahmen zu erarbeiten und umzusetzen, analysiert die Task Force Umwelt die Fertigungsprozesse und Fabrikversorgungsanlagen sowie die Ressourcen- und Energieströme an den Konzernstandorten und bewertet die jeweiligen Auswirkungen der Effizienzmaßnahmen. Mit den Erfahrungen aus den Analysen in mehreren Marken und Regionen kann das Team systematisch den Maßnahmentransfer stärken und vorantreiben.
In einem IT-gestützten System erfassen und katalogisieren wir Umweltmaßnahmen, die wir für einen konzernweiten Best-Practice-Austausch zur Verfügung stellen. Im Berichtsjahr wurden in diesem System rund 1.500 umgesetzte Maßnahmen im Bereich Umwelt und Energie dokumentiert, die der Verbesserung der Infrastruktur und der Produktionsprozesse von Pkw und leichten Nutzfahrzeugen dienen. Diese Aktivitäten lohnen sich in ökologischer und ökonomischer Hinsicht.
Mit vielen effektiven und innovativen Maßnahmen wurde auch im Berichtsjahr wieder die Reduzierung der Umweltindikatoren vorangetrieben, wobei zugleich Produktionsprozesse verbessert wurden.
WESENTLICHE UMWELTKENNZAHLEN FÜR DIE PRODUKTION IM VOLKSWAGEN KONZERN1
Green Logistics
Zur ökologischen Ausrichtung des Volkswagen Konzerns trägt die Logistik bei, indem die gesamte Transportkette im Hinblick auf Emissionen analysiert wird. Die Initiative Green Logistics fördert alternative Fortbewegungsmittel sowie nachhaltige, energieeffiziente Transportsysteme.
Aufbauend auf dem im September 2017 mit dem LNG-Truck-Day begonnenen Dialog von der Konzern-Logistik und Scania mit Spediteuren, Behörden und Mineralölgesellschaften wird das Thema LNG-Lkw (LNG, Liquefied Natural Gas – Erdgas) nun umgesetzt. Ziel ist es, dass LNG-Lkw künftig auf vielen Strecken fahren und dafür das entsprechende Tankstellennetz vorhanden ist. Die Konzern-Logistik plant, mit den Dienstleistern mittelfristig in Norddeutschland ungefähr 100 LNG-Lkw einzusetzen. Die ersten Lkw fahren seit Januar 2019 auf den Straßen.
Mit Blick auf die Transportleistung ist die Seeschifffahrt ein weiterer wesentlicher Ansatzpunkt, um CO2-Emissionen einzusparen. Ab Mitte 2019 stellt die Volkswagen Konzern-Logistik zwei mit Flüssigerdgas betriebene Charterschiffe in den Dienst. Die emissionsarmen LNG-Schiffe werden zwischen Europa und Nordamerika Fahrzeugmodelle des Volkswagen Konzerns befördern.
Damit unsere Mitarbeiter den Weg zur Erreichung unserer Umweltziele bestmöglich unterstützen und mitgestalten können, sind interne Schulungen zum Thema Green Logistics sowie Vorträge an Hochschulen fester Bestandteil der Ausbildung.